FOB price: About $13.90/kg
High conductivity Copper casting plays a crucial role in industries requiring superior electrical and thermal performance. As a specialized foundry-manufacturer, we offer precision casting solutions using high-purity Copper grades to ensure optimal conductivity, machinability, and durability. A1 Metallics is a leading manufacturer and supplier of Copper and Bronze castings at their foundry in Jamnagar, India. We specialize in Copper Castings with a big focus on high conductivity pure Copper casting and Copper machined parts. High conductivity Copper casting represents a specialized segment of the metal casting industry, demanding precise control and expertise to achieve optimal electrical performance. As a critical process for manufacturing electrical components, our foundry specializes in producing Copper Castings with conductivity ratings between 85-98% IACS (International Annealed Copper Standard). By utilizing advanced casting techniques and rigorous quality control measures, we maintain the metal’s inherent conductivity while forming complex geometries that would be difficult or uneconomical to produce through other manufacturing methods. Our facility combines traditional casting expertise with modern metallurgical controls to serve industries ranging from power distribution to electric vehicle manufacturing, where high electrical conductivity and mechanical integrity are paramount. Our Copper Casting Foundry at Jamnagar in India is a modern state-of-the-art facility with latest casting equipment and testing instruments.
High Conductivity Copper Casting -Grades and Specifications
US Copper Alloy Designations
- C10100 (OFE): 101% IACS, Oxygen-Free Electronic
- C10200 (OF): 100% IACS, Oxygen-Free
- C11000: 100% IACS, Electrolytic Tough Pitch (ETP)
- C12200: 98% IACS, Phosphorus Deoxidized, High Residual Phosphorus
- C10100 (Oxygen-Free Electronic Copper – OFE) – 99.99% pure, excellent electrical conductivity.
- C11000 (Electrolytic Tough Pitch – ETP) – 99.90% pure, standard for electrical applications.
- C12000, C12200 (Deoxidized Copper – DLP/DHP) – Enhanced weldability, lower conductivity.
- C18150 (Copper-Chromium-Zirconium) – Used for high-performance electrical applications.
- Equivalents: CW008A (EN), Cu-ETP (DIN), Cu-OFE (ISO).
International Standards
- EN CW004A (Cu-ETP)
- EN CW008A (Cu-OF)
- EN CW009A (Cu-OFE)
- JIS C1020
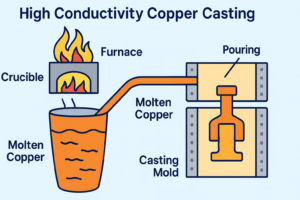
High Conductivity Copper Casting Process
 Sand Casting
- Ideal for complex geometries and prototype runs
- Typical tolerances: ±0.8mm for first 25mm, ±0.3mm for each additional 25mm
- Surface finish: 250-900 RMS
Permanent Mold Casting
- Superior surface finish and dimensional accuracy
- Typical tolerances: ±0.4mm for first 25mm
- Surface finish: 125-250 RMS
- Ideal for medium to high volume production
Centrifugal Casting
- Excellent for cylindrical components
- Enhanced density and mechanical properties
- Typical tolerances: ±0.5mm on diameter
- Surface finish: 125-250 RMS
Shell Mold Casting
- Better dimensional accuracy than sand casting
- Typical tolerances: ±0.4mm
- Surface finish: 150-300 RMS
Machining Services
- CNC Milling: 5-axis capability
- Threading: Metric and Imperial standards
- Surface grinding
- EDM capabilities for complex features
- Typical machining tolerances: ±0.025mm
Electrical Conductivity
- Measured in % IACS (International Annealed Copper Standard)
- Pure copper = 100% IACS
- Typical cast components: 85-98% IACS depending on alloy
- Temperature coefficient: 0.393% per °C
Surface Finishes
- As-cast
- Machined
- Polished (Ra 0.4-1.6μm)
- Plated options:
- Silver
- Tin
- Nickel
- Gold (for specialized applications)
Common Applications
Electrical Industry
- Bus bars, Switchgear contacts
- Terminal blocks
- High-current connectors
- Ground straps
- Circuit breaker components
Power Generation
- Generator components
- Transformer parts
- Switchgear components
Transportation
- Electric vehicle charging components
- Railway electrification parts
- Power distribution elements
Why High Conductivity Copper Casting is a Niche Market
- Specialized expertise required for:
- Temperature control during casting
- Oxygen content management
- Porosity prevention
- Conductivity maintenance
- Complex equipment requirements:
- Protective atmosphere systems
- Precise temperature controls
- Specialized melting equipment
- Quality control challenges:
- Conductivity testing
- Porosity inspection
- Oxide inclusion prevention
Frequently Asked Questions about Copper Castings-
Q: What is the minimum wall thickness possible on High Conductivity Copper Casting? A: 3mm for sand casting, 2mm for permanent mold casting
Q: What is the maximum Copper casting weight? A: Up to 500kg for sand casting, 50kg for permanent mold casting
Q: How does conductivity compare to wrought copper? A: Cast copper typically achieves 85-98% of wrought copper conductivity
Q: What are typical lead times for High Conductivity Copper Casting? A: 4-6 weeks for new tooling, 2-3 weeks for repeat orders
Q: Are RoHS compliant options available for High Conductivity Copper Casting? A: Yes, all high conductivity copper grades are inherently RoHS compliant
Our casting foundry offers- Brass casting, Bronze casting, Copper casting with a focus on following-
- Bronze casting
- Brass casting
- Non-ferrous casting
- Bronze Transformer Ground Clamps Transformer ground Connectors Tank ConnectorsÂ
- Copper alloy casting
- Metal casting foundry
- LG2 Bronze CDA 836 Alloy Gunmetal casting
- Bronze Machined Casting
- Investment casting copper
- Die casting copper
- Green sand casting
- Continuous casting copper
- Copper melting furnace
- Ingot casting
- Metal foundry services
Material Properties:
- High electrical conductivity
- Thermal conductivity
- Corrosion resistance
- Oxygen-free copper
- Pure copper
- IACS conductivity
- Copper grades
- ETP copper
- Deoxidized copper
- Cast copper properties
- Copper microstructure
Applications & Industries:
- Electrical components
- Bus bar manufacturing
- Power distribution
- Transformer parts
- Switchgear components
- Marine applications
- Industrial machinery
- Railway electrification
- Electric vehicle parts
- Copper terminals
- Electrical connectors
- Power transmission
Quality & Standards:
- ISO copper standards
- ASTM standards
- Metallurgical testing
- NDT testing copper
- Porosity testing
- Conductivity testing
- Quality certification
- Material certification
- RoHS compliance
- Copper purity testing
Processing & Finishing:
- Copper machining
- Surface finishing
- Heat treatment copper
- Copper plating
- Silver plating
- Tin plating
- CNC machining copper
- Copper polishing
- Threading copper
- Copper milling
- Surface treatment
Understanding High Conductivity Copper Casting – Comprehensive Technical Guide
What makes High Conductivity Copper Casting unique in foundry operations? High Conductivity Copper Casting is specialized metal casting process focused on producing components with superior electrical conductivity. The High Conductivity Copper Casting process requires:
- Minimum conductivity of 100% IACS
- Oxygen content below 0.001%
- Total impurity levels less than 0.03%
- Phosphorus content maximum 0.003% Our High Conductivity Copper Casting facility specializes in grades C10100, C10200, and C10300.
What melting parameters ensure optimal High Conductivity Copper Casting quality? Our High Conductivity Copper Casting process maintains strict control over:
- Melting temperature range: 1065°C – 1083°C
- Pouring temperature: 1120°C – 1150°C
- Superheat control: ±5°C maximum variation The High Conductivity Copper Casting requires protective atmosphere:
- Nitrogen with 2-4% Hydrogen
- Argon for premium grades
- Maximum oxygen content 1 ppm
What specialized equipment is required for High Conductivity Copper Casting? High Conductivity Copper Casting demands specific equipment:
- Induction Furnace for High Conductivity Copper Casting:
- Frequency: 1-3 kHz
- Power density: 300-400 kW/ton
- Crucible type: High-purity graphite
- Temperature Control Systems:
- Digital pyrometry
- Immersion thermocouples
- Continuous monitoring systems
- Atmosphere Control for High Conductivity Copper Casting:
- Gas analysis systems
- Flow control: 15-20 CFH
- Pressure monitoring: ±0.5 inH2O
What mold requirements are crucial for High Conductivity Copper Casting? High Conductivity Copper Casting mold specifications include:
- Material Options for High Conductivity Copper Casting:
- Graphite molds for continuous casting
- Water-cooled copper molds
- Ceramic shells for investment casting
- Temperature Control in High Conductivity Copper Casting:
- Preheat: 150-200°C
- Cooling rate: 100-150°C/min
- Thermal gradient control
- Surface Finish Requirements:
- Roughness Ra < 0.8μm
- Specific coatings for High Conductivity Copper Casting
What quality control measures ensure premium High Conductivity Copper Casting? Our High Conductivity Copper Casting quality protocols include:
- Chemical Analysis for High Conductivity Copper Casting:
- Spectrographic analysis
- Oxygen determination
- Hydrogen content measurement
- Physical Testing of High Conductivity Copper Castings:
- Conductivity testing (Eddy current)
- Density measurement
- Porosity analysis
- Mechanical Properties Verification:
- Tensile strength: 250-280 MPa
- Elongation: 45-55%
- Hardness: 40-65 HRB
How is defect prevention managed in High Conductivity Copper Casting? High Conductivity Copper Casting defect prevention includes:
- Gas Porosity Control in High Conductivity Copper Casting:
- Vacuum degassing system operation
- Proper venting design implementation
- Continuous gas content monitoring
- Inclusion Prevention:
- Ceramic foam filtration systems
- Electromagnetic slag control
- Specialized flux application
- Shrinkage Control Methods:
- Computer-simulated gating design
- Optimized riser placement
- Real-time thermal analysis
What post-casting treatments are essential for High Conductivity Copper Casting? High Conductivity Copper Casting post-processing includes:
- Heat Treatment for High Conductivity Copper Castings:
- Annealing temperature: 350-400°C
- Controlled cooling rate: 50-75°C/hour
- Protective atmosphere maintenance
- Surface Treatment:
- Sulfuric acid pickling
- Bright dipping in nitric acid solution
- Protective organic coating application
- Dimensional Control:
- Automated straightening systems
- CNC surface machining
- Laser scanning verification
What environmental controls are required for High Conductivity Copper Casting? High Conductivity Copper Casting environment management includes:
- Foundry Atmosphere Requirements:
- Temperature: 20-25°C
- Humidity: 45-55%
- Dust control: <10 mg/m³
- Waste Management in High Conductivity Copper Casting:
- Slag classification and handling
- Emissions scrubbing systems
- Closed-loop water treatment
- Material Recovery Protocols:
- Grade-specific scrap segregation
- Impurity-controlled recycling
- Digital tracking systems
What documentation supports High Conductivity Copper Casting production? High Conductivity Copper Casting documentation includes:
- Process Records:
- Real-time melt chemistry data
- Digital temperature logging
- Atmospheric condition monitoring
- Testing Certificates for High Conductivity Copper Casting:
- IACS conductivity verification
- Full chemical composition analysis
- Mechanical property certification
- Quality Assurance Documentation:
- Ultrasonic testing results
- X-ray inspection reports
- Heat lot traceability records
What safety protocols are specific to High Conductivity Copper Casting? High Conductivity Copper Casting safety requirements include:
- Personal Protection for High Conductivity Copper Casting:
- Aluminized protective suits
- Powered air-purifying respirators
- Face shields with gold reflective coating
- Process Safety Controls:
- Automated molten metal handling
- Inert gas monitoring systems
- Emergency cooling protocols
- Environmental Safety in High Conductivity Copper Casting:
- Multi-stage ventilation systems
- Continuous emissions monitoring
- Hazardous material containment
What are the facility requirements for High Conductivity Copper Casting? High Conductivity Copper Casting facility needs include:
- Infrastructure:
- Reinforced concrete foundations
- Overhead crane systems: 10-50 ton capacity
- Climate-controlled production areas
- Utility Systems:
- High-capacity electrical supply: 2000-4000 kVA
- Cooling water systems: 200-400 GPM
- Compressed air: 100-150 PSI
- Material Handling:
- Automated charging systems
- Specialized ladle designs
- Computer-controlled pouring equipment