High Quality Aluminum Hotline Clamps and Bronze Hotline Clamps.


Bronze and Aluminium Hotline Clamps: Essential Components for Power Distribution
Hotline clamps, also known as live-line clamps or hot stick clamps, are critical tools in the electrical utility industry, enabling secure connections to energized power lines without interrupting service. Used primarily for maintenance, repairs, or temporary connections, these clamps ensure safety, reliability, and efficiency in overhead power distribution systems. Bronze and aluminium hotline clamps are the most common types, each offering unique properties suited to specific applications. This article explores their material grades, sizes, conductor compatibility, and key features, drawing on their role in modern electrical grids.
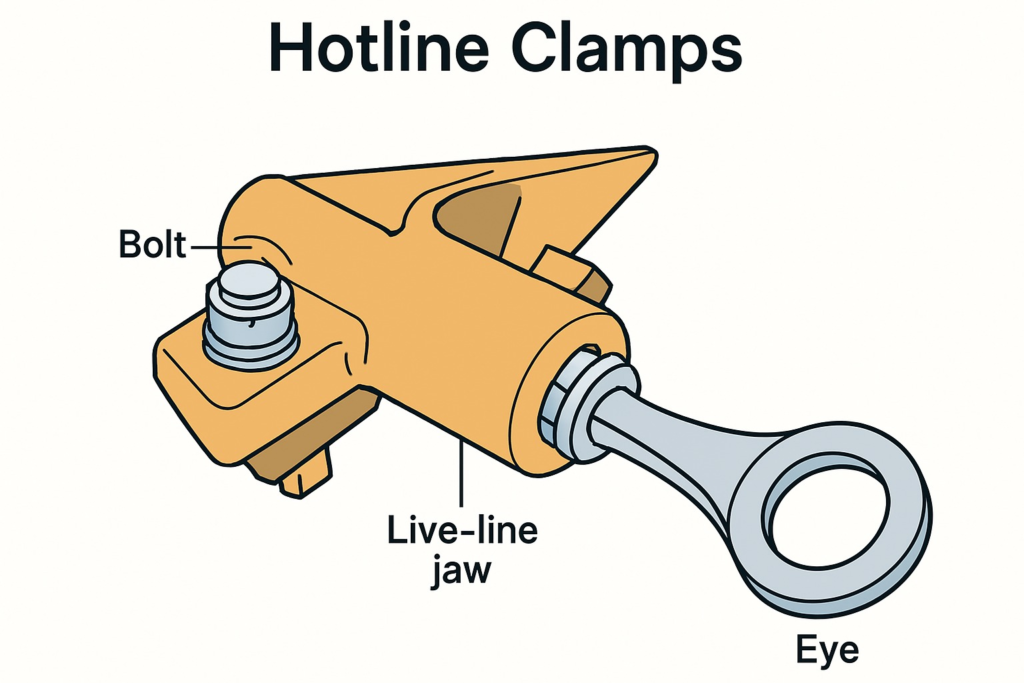
Bronze Hotline Clamps
Bronze hotline clamps are widely favored for their durability, conductivity, and resistance to environmental challenges. These clamps are typically used in scenarios requiring robust connections, such as connecting tap lines to transformers or supporting live-line maintenance.
Material Grades
Bronze hotline clamps are crafted from high-strength bronze alloys to withstand electrical and mechanical stresses. Common grades include:
- CDA 955 (Aluminium Bronze): Contains 10-11% aluminium, offering high strength, excellent corrosion resistance, and good conductivity. Ideal for heavy-duty applications.
- CDA 836 (Leaded Red Brass): Includes lead for improved machinability, with decent conductivity and corrosion resistance.
- CDA 844 and 956: Variants with slight compositional tweaks for enhanced durability in harsh conditions. These alloys provide a balance of electrical performance and mechanical resilience, making them suitable for outdoor environments exposed to moisture, salt, or industrial pollutants.
Sizes and Configurations
Bronze hotline clamps come in various sizes to accommodate different conductor types and current loads. Typical configurations include:
- Type A (Light Duty): For smaller conductors and lower current applications.
- Type B (Medium Duty): Versatile for distribution lines with moderate loads.
- Type C (Heavy Duty): Designed for high-current, high-voltage scenarios. Standard clamp sizes range from compact designs (e.g., 2 inches in length) for secondary lines to larger models (up to 5 inches) for primary distribution. Eyebolts, often made from stainless steel or C955 bronze, ensure secure fastening and compatibility with hot sticks for safe installation.
Conductor Sizes
Bronze hotline clamps are engineered to grip a wide range of conductors, including copper, aluminium, and ACSR (Aluminium Conductor Steel Reinforced). Common conductor size compatibility includes:
- American Wire Gauge (AWG): 8 AWG to 4/0 AWG.
- Circular Mil Area (CMA): 250 kcmil to 1000 kcmil.
- Diameter Range: 0.1 inches to 2.5 inches, with some models featuring adjustable jaws or removable liners to handle variations without damaging conductors. These clamps often use serrated jaw liners to enhance grip while minimizing conductor wear, ensuring stable connections under thermal expansion or vibration.
Key Features
- Superior Conductivity: Bronze’s low resistance ensures minimal power loss, critical for efficient transmission.
- Corrosion Resistance: Naturally forms a protective oxide layer, ideal for coastal or humid environments.
- High Current Capacity: Handles 100 to 1000 amperes, depending on the model.
- Safety Design: Bolt-pressure mechanisms and smooth, contoured surfaces reduce corona discharge and simplify installation with insulated tools.
- Standards Compliance: Meets ANSI C119.4, IEEE 1243, and NESC guidelines for reliability and safety.
Bronze clamps excel in applications requiring longevity and resilience, such as utility networks in harsh climates or high-load industrial settings. However, they are heavier and costlier than aluminium alternatives, which influences their use in budget-conscious projects.
Aluminium Hotline Clamps
Aluminium hotline clamps are valued for their lightweight design, cost-effectiveness, and compatibility with aluminium-based conductors. They are often chosen for temporary connections, bypass circuits, or regions prioritizing weight reduction.
Material Grades
Aluminium hotline clamps are made from high-strength aluminium alloys optimized for electrical and structural performance. Common grades include:
- 6061-T6: A versatile alloy with good strength, corrosion resistance, and weldability. Widely used for general-purpose clamps.
- 7075-T6: Higher strength for demanding applications, though less corrosion-resistant than 6061.
- CDA 955 (Aluminium Bronze): Occasionally used for hybrid clamps combining aluminium’s lightness with bronze’s durability. These alloys are often tin-plated to prevent galvanic corrosion when paired with copper conductors, enhancing longevity in mixed-metal systems.
Sizes and Configurations
Aluminium hotline clamps are designed for flexibility, with sizes tailored to conductor dimensions and installation needs. Common types include:
- C-Shaped Clamps: Lightweight with threaded eyes for hot stick attachment.
- Bolted Clamps: Use stainless steel bolts for secure fastening.
- Stirrup Clamps: Feature a stirrup-like design for specific tap connections. Sizes typically range from 1.5 inches for small distribution lines to 4 inches for larger setups. Their modular designs often allow for range-taking capability, accommodating slight conductor size variations within a single clamp.
Conductor Sizes
Aluminium clamps are optimized for aluminium and ACSR conductors but can handle copper with proper plating. Supported conductor sizes include:
- AWG: 6 AWG to 4/0 AWG.
- CMA: 167 kcmil to 795 kcmil.
- Diameter Range: 0.16 inches to 2 inches, with self-aligning jaws to ensure optimal contact across sizes. These clamps are particularly effective in systems where aluminium conductors dominate, reducing weight and cost without sacrificing performance.
Key Features
- Lightweight Design: Up to 50% lighter than bronze, easing installation and reducing pole stress.
- Cost-Effective: Lower material and production costs make them ideal for large-scale projects.
- Corrosion Resistance: Enhanced by anodizing or tin-plating, though less robust than bronze in extreme conditions.
- Ease of Use: One-handed operation with hot sticks, thanks to ergonomic designs and low weight.
- Standards Compliance: Adheres to ASTM B117 (salt spray test) and ANSI C119.4 for consistent performance.
Aluminium clamps shine in applications prioritizing efficiency and budget, such as rural distribution networks or temporary repairs. However, they may require more frequent inspections in corrosive environments due to aluminium’s lower resistance compared to bronze.
Comparing Bronze and Aluminium Hotline Clamps
Feature | Bronze Hotline Clamps | Aluminium Hotline Clamps |
---|---|---|
Material Grades | CDA 955, 836, 844, 956 | 6061-T6, 7075-T6, CDA 955 (hybrid) |
Weight | Heavier (e.g., 1-2 lbs) | Lighter (e.g., 0.5-1 lb) |
Conductivity | Excellent, minimal loss | Good, slightly higher resistance |
Corrosion Resistance | Superior, ideal for harsh environments | Good, requires plating in mixed-metal use |
Cost | Higher | Lower |
Conductor Sizes | 8 AWG to 4/0 AWG, 0.1-2.5 inches | 6 AWG to 4/0 AWG, 0.16-2 inches |
Applications | Heavy-duty, long-term, high-load | Temporary, lightweight, cost-sensitive |
Applications and Selection Considerations
Both clamp types serve critical roles in:
- Live-Line Maintenance: Enabling repairs without power outages.
- Temporary Connections: Supporting bypass circuits or testing equipment.
- Transformer Taps: Connecting tap lines to transformers for voltage conversion.
- Emergency Repairs: Gripping damaged conductors until permanent fixes are made.
When choosing between bronze and aluminium:
- Environment: Opt for bronze in coastal or industrial areas; aluminium suffices in milder climates.
- Conductor Type: Match clamp material to conductor material to avoid galvanic corrosion (e.g., aluminium clamps for ACSR).
- Load Requirements: Use bronze for high-current, long-term connections; aluminium for lighter loads.
- Budget: Aluminium offers savings for large deployments, while bronze justifies its cost in critical infrastructure.
- Standards: Ensure compliance with regional codes (e.g., IEEE, NESC) and conductor compatibility.
Conclusion
Bronze and aluminium hotline clamps are indispensable for maintaining safe, reliable power distribution. Bronze clamps, with grades like CDA 955 and 836, offer unmatched durability and conductivity for demanding applications, accommodating conductors from 8 AWG to 4/0 AWG. Aluminium clamps, using alloys like 6061-T6, provide a lightweight, cost-effective alternative, handling conductors from 6 AWG to 4/0 AWG with ease. By understanding their material properties, sizes, and conductor compatibility, utility professionals can select the right clamp for their specific needs, ensuring efficient power flow and worker safety. As grids evolve, both clamp types will remain vital, balancing performance with practical considerations in an ever-changing energy landscape.